Measuring/using buckling strength-new info
-
- Coach
- Posts: 1318
- Joined: Thu Nov 13, 2008 3:01 am
- Division: C
- State: CO
- Has thanked: 0
- Been thanked: 3 times
Measuring/using buckling strength-new info
Set up new topic so it wouldn't get lost in the general Towers B/B thread.
A very important update/refinement and clarification on the discussion (in the Towers B/C thread) of buckling strength, and testing/measuring the buckling strength (“BS”) of 36”sticks for tower design and the selection of sticks based on this testing for use in a tower.
I’d discussed in an early post in the Towers B/C thread how “S.O. is all about learning and applying science; the wood structures events are about learning and applying engineering , and engineering is about extracting from the full complexity of the underlying/relevant science; getting to and applying a set of approximations that are close enough to ‘work’ for what you’re trying to do- build the lightest structure you can to carry a 15kg load.” While the discussion, information, and approach/process developed in the thread may seem very complex to some, I’ve tried to keep things… as simple as they can be ‘to work’; to provide everyone with a framework that will allow you to objectively/quantitatively design a competitive tower (the configuration-how to figure out what intervals to brace the legs at, and wood selection- what a) buckling strength (tested in 36” sticks) will work in various bracing interval options), and b) density/stick weight of 1/8 balsa will likely get you get you to a ‘target’/’design’ buckling strength.
In this post, we’re going to go a bit further ‘down the rabbit hole’, into the next couple of layers of… complexity; the ‘full underlying science’ of how buckling works, and how that understanding/science applies to testing buckling strength, and using that test data to calculate what wood, braced at what intervals “should work” for legs in a tower.
The past discussion lays out an approach of taking a 36” stick, putting it vertically on a scale,” holding the top, and, pushing straight down”, and measuring/reading the buckling strength – the load the scale shows when the stick buckles- deflects a bit, into a bowed condition. With that value, the measured buckling strength at 36”, you can then easily calculate, using an inverse square table, the buckling strength at shorter column lengths/intervals. That allows you to calculate/evaluate the buckling strength at various ‘braced intervals’ – the distance between bracing points on the legs of the tower.
In presenting this approach/technique, I have realized my description of how to hold the stick to “push down” from the top of the stick was unclear. My sincere apologies for lack of clarity/correctness in this. I think/hope this post will provide clarity and completeness.
In discussions in the Towers B/C thread, on page 18, BananaPirate noted that the 36” BS he/she was measuring was a lot less than the number I was seeing. I said we were seeing a 36” BS for a 1.5gr stick at about 80 grams; BananaPirate was seeing ‘nothing close to that.’ Reviewing Euler’s Buckling Theorem in detail, and doing some more testing work, I believe I correctly understand where the differences are coming from.
Depending on how you hold the top of the stick, you’ll get significantly different results for the buckling strength at 36”. It has to do with two factors referred to as the “end (or ‘boundary’ condition” and the “effective length” of the column/stick being tested. These are the next two layers of complexity, the underlying science around buckling behavior, we need to get into to understand and resolve this issue.
To cut to the conclusions (before more detailed discussion);
First I believe the numbers I’ve been seeing and reporting for 36” BS vs (1/8 x 1/8 balsa) stick weights are approximately correct. These numbers come from holding the top of the stick firmly between two fingers. However, if you do 36” buckling strength testing by just placing one finger on the top of the stick, and pushing down, not holding the top with/between two fingers, the buckling strength you’ll measure at 36” (when you push down on the end of the stick) will be approximately ½ the value I’ve been seeing/reporting. This difference is because of the difference in ‘end conditions’ in these two methods.
Second, I believe a) the correct/appropriate/conservative value to use for 36” BS (which is then used to calculate the higher BS in shorter braced intervals) is twice (2.0 times) the value measured when pushing down with one finger, and b) it is likely this factor may well be as much as/may approach 2.3 times.
If you go to these two links, you’ll see a discussion of how, in buckling behavior, the ‘effective length’ of a column is affected by the ‘end conditions.’ Both show a table with effective length values for various sets of end conditions. The three we’re concerned with are:
-“Pinned” or ”hinged” end conditions at both ends; as the stick bends when it bows into buckling, the end is free to rotate/follow the deflection of the stick as it bows,
-“Pinned” or “hinged” end conditions at one and “fixed” or “clamped” end conditions at the other end; the end of the stick is held firmly in-place- as if the end were glued to a solid plate – as the stick bows into buckling, the very end can’t rotate/lift off the plate, and,
-“Fixed” or “clamped” end conditions at both ends.
https://en.wikipedia.org/wiki/Buckling
http://www.efunda.com/formulae/solid_me ... olumns.cfm
First, let’s just look at the values in the first link for the “effective length” ( which are referred to as “K-factors”) of a column.
-For both ends pinned (hinged, free to rotate), = 1.0.
-For both ends fixed, = 0.50.
-For one end fixed and the other end pinned, ≈ 0.7071.
So what does this mean? When you place one end of a stick on the scale, and push down with one finger on the top, you have/create what are referred to as “pinned” or ”hinged” end conditions at both ends; as the stick bends when it bows into buckling, the end is free to rotate/follow the deflection of the stick as it bows.. However, if you hold the top portion tightly, you prevent/limit the ability of the upper end to rotate. This is referred to as a “fixed” or “clamped” end condition.
In the ‘effective length’ values above, you’ll see that the effective length of a column tested with pinned end conditions at both ends is 1, while the effective length of a column (of the same length) with a pinned end condition at one end, and a fixed/clamped end condition is approximately 0.7071.
So, remembering how we calculate the inverse square relationship, to see what the BS for a shorter section of a ‘full length’ stick is; it is 1 over the proportion (of the shorter section to the full length stick), i.e., 1 over 0.7071 squared, which is 2.00. A piece that is 0.7071 of a longer piece will theoretically have twice the BS of the longer piece. That means that if a longer/’full length’ stick is tested with pinned/pinned end conditions (pushing down on the top with one finger), that same stick tested with pinned/fixed end conditions will/should test at twice the BS.
Looking at the situation/value for pinned/pinned end conditions (an effective length of 0.5), that tells us that if a stick is tested (pushing down with one finger), that same stick tested with fixed/fixed end conditions will be 1 over 0.5 squared, which is 4 times the pinned-pinned test value. So, we see that the 36” buckling strength used to calculate the higher buckling strength of shorter braced intervals is somewhere between 2.0 and 4.0 times the buckling strength measured by pushing down on the end of a 36” stick. That’s a….pretty wide range. You can see why I said that using the 2.0 value is ‘conservative.’ Going to the next level of complexity gives us a way to narrow that range.
In the second link, we see the table for effective length factors for various end conditions has two columns, a “theoretical” value, and an “engineering effective length.” The engineering effective length recognizes that in real structures, a) end conditions aren’t perfect (exactly meeting all the assumptions that go into calculating them), and many other factors/complexities are at work in real structures. This link:
http://freeit.free.fr/Structure%20Engin ... ook/17.pdf
gives you, in mind-boggling depth, a sense of just how complicated these factors (and the associated math) really are when you dig into the science. See discussion in Sections 17.2 – 17.4 for effective length, and in Section 17.8 there is a discussion of bracing systems.. The key thing is Figure 17.2 on page 5. On page 5, this figure is explained as follows; “Figure 17.2 summarizes the theoretical K-factors (effective length) for columns with some idealized end conditions. The recommended K-factors are also shown in Figure 17.2 for practical design applications. Since actual column conditions seldom comply fully with idealized conditions used in buckling analysis, the recommended K-factors are always equal to or greater than their theoretical counterparts.”
These K-factors are the same shown in the second link. Since we’re dealing with real structures, it seems appropriate to use the “engineering”/”recommended” “K-“/”engineering effective length” factors.
Doing this, the ‘engineering’ K-factor for fixed-pinned end conditions is 0.8 (vs the 0.7071 theoretical factor we discussed and calculated from above). Doing the same calculation we did for 0.7071 ( which becomes 1 over 0.8 squared), we see that instead of multiplying the (pinned-pinned) push-down BS by 2.0, we would want to use a factor of 1.56. Looking at fixed-fixed end conditions, the ‘engineering’ K-factor is 0.65 (vs. the theoretical K-factor is 0.5. Doing the same calculation again (this time, 1 over 0.65 squared), we see that instead of multiplying the (pinned-pinned) push-down BS by 4.0, we want to use a factor of 2.37). So, instead of a range between 2.0 and 4.0 for the factor to adjust our 36” pushdown test data, we’re now at a range of 1.56 (if the end conditions of a braced leg segment are pinned-fixed) to 2.37 (if the end conditions of a braced leg segment are fixed-fixed).
So, the final question becomes, what are the end conditions of a braced section of leg in a tower? How does a tested 36” BS value (using single finger pushdown/pinned/pinned end conditions) correctly translate to a calculated BS of a leg section between two braced points? The answer is, I’m not sure, and the math to try to figure it is way, way over my head. I do know it is… effectively.. somewhere between.
When using the ‘ladders and Xs’ bracing approach I’ve detailed previously, it does seems like the braced leg segments have… something close to fixed end conditions at both ends (braced points), and it is pretty clear that neither end is under anything close to pinned end condition. And that’s why I’ve come to the conclusion that the correct approximation of the ‘real answer’ (what factor do you want to multiply 36” single finger pushdown measured buckling strength by to get to a buckling strength to use in calculating the buckling strength of braced leg segments in your tower) is somewhere between 2.0 and 2.3.
Only testing, in real towers, is going to give us insight into ‘the real answer.’ If the end conditions at braced points are really close to “fixed”, then the “best” tower weight estimates we’ve been tossing around out are a bit high; B-towers in the low to mid 6 gram, and C-towers at or slightly below 7.5 grams may be possible……
A very important update/refinement and clarification on the discussion (in the Towers B/C thread) of buckling strength, and testing/measuring the buckling strength (“BS”) of 36”sticks for tower design and the selection of sticks based on this testing for use in a tower.
I’d discussed in an early post in the Towers B/C thread how “S.O. is all about learning and applying science; the wood structures events are about learning and applying engineering , and engineering is about extracting from the full complexity of the underlying/relevant science; getting to and applying a set of approximations that are close enough to ‘work’ for what you’re trying to do- build the lightest structure you can to carry a 15kg load.” While the discussion, information, and approach/process developed in the thread may seem very complex to some, I’ve tried to keep things… as simple as they can be ‘to work’; to provide everyone with a framework that will allow you to objectively/quantitatively design a competitive tower (the configuration-how to figure out what intervals to brace the legs at, and wood selection- what a) buckling strength (tested in 36” sticks) will work in various bracing interval options), and b) density/stick weight of 1/8 balsa will likely get you get you to a ‘target’/’design’ buckling strength.
In this post, we’re going to go a bit further ‘down the rabbit hole’, into the next couple of layers of… complexity; the ‘full underlying science’ of how buckling works, and how that understanding/science applies to testing buckling strength, and using that test data to calculate what wood, braced at what intervals “should work” for legs in a tower.
The past discussion lays out an approach of taking a 36” stick, putting it vertically on a scale,” holding the top, and, pushing straight down”, and measuring/reading the buckling strength – the load the scale shows when the stick buckles- deflects a bit, into a bowed condition. With that value, the measured buckling strength at 36”, you can then easily calculate, using an inverse square table, the buckling strength at shorter column lengths/intervals. That allows you to calculate/evaluate the buckling strength at various ‘braced intervals’ – the distance between bracing points on the legs of the tower.
In presenting this approach/technique, I have realized my description of how to hold the stick to “push down” from the top of the stick was unclear. My sincere apologies for lack of clarity/correctness in this. I think/hope this post will provide clarity and completeness.
In discussions in the Towers B/C thread, on page 18, BananaPirate noted that the 36” BS he/she was measuring was a lot less than the number I was seeing. I said we were seeing a 36” BS for a 1.5gr stick at about 80 grams; BananaPirate was seeing ‘nothing close to that.’ Reviewing Euler’s Buckling Theorem in detail, and doing some more testing work, I believe I correctly understand where the differences are coming from.
Depending on how you hold the top of the stick, you’ll get significantly different results for the buckling strength at 36”. It has to do with two factors referred to as the “end (or ‘boundary’ condition” and the “effective length” of the column/stick being tested. These are the next two layers of complexity, the underlying science around buckling behavior, we need to get into to understand and resolve this issue.
To cut to the conclusions (before more detailed discussion);
First I believe the numbers I’ve been seeing and reporting for 36” BS vs (1/8 x 1/8 balsa) stick weights are approximately correct. These numbers come from holding the top of the stick firmly between two fingers. However, if you do 36” buckling strength testing by just placing one finger on the top of the stick, and pushing down, not holding the top with/between two fingers, the buckling strength you’ll measure at 36” (when you push down on the end of the stick) will be approximately ½ the value I’ve been seeing/reporting. This difference is because of the difference in ‘end conditions’ in these two methods.
Second, I believe a) the correct/appropriate/conservative value to use for 36” BS (which is then used to calculate the higher BS in shorter braced intervals) is twice (2.0 times) the value measured when pushing down with one finger, and b) it is likely this factor may well be as much as/may approach 2.3 times.
If you go to these two links, you’ll see a discussion of how, in buckling behavior, the ‘effective length’ of a column is affected by the ‘end conditions.’ Both show a table with effective length values for various sets of end conditions. The three we’re concerned with are:
-“Pinned” or ”hinged” end conditions at both ends; as the stick bends when it bows into buckling, the end is free to rotate/follow the deflection of the stick as it bows,
-“Pinned” or “hinged” end conditions at one and “fixed” or “clamped” end conditions at the other end; the end of the stick is held firmly in-place- as if the end were glued to a solid plate – as the stick bows into buckling, the very end can’t rotate/lift off the plate, and,
-“Fixed” or “clamped” end conditions at both ends.
https://en.wikipedia.org/wiki/Buckling
http://www.efunda.com/formulae/solid_me ... olumns.cfm
First, let’s just look at the values in the first link for the “effective length” ( which are referred to as “K-factors”) of a column.
-For both ends pinned (hinged, free to rotate), = 1.0.
-For both ends fixed, = 0.50.
-For one end fixed and the other end pinned, ≈ 0.7071.
So what does this mean? When you place one end of a stick on the scale, and push down with one finger on the top, you have/create what are referred to as “pinned” or ”hinged” end conditions at both ends; as the stick bends when it bows into buckling, the end is free to rotate/follow the deflection of the stick as it bows.. However, if you hold the top portion tightly, you prevent/limit the ability of the upper end to rotate. This is referred to as a “fixed” or “clamped” end condition.
In the ‘effective length’ values above, you’ll see that the effective length of a column tested with pinned end conditions at both ends is 1, while the effective length of a column (of the same length) with a pinned end condition at one end, and a fixed/clamped end condition is approximately 0.7071.
So, remembering how we calculate the inverse square relationship, to see what the BS for a shorter section of a ‘full length’ stick is; it is 1 over the proportion (of the shorter section to the full length stick), i.e., 1 over 0.7071 squared, which is 2.00. A piece that is 0.7071 of a longer piece will theoretically have twice the BS of the longer piece. That means that if a longer/’full length’ stick is tested with pinned/pinned end conditions (pushing down on the top with one finger), that same stick tested with pinned/fixed end conditions will/should test at twice the BS.
Looking at the situation/value for pinned/pinned end conditions (an effective length of 0.5), that tells us that if a stick is tested (pushing down with one finger), that same stick tested with fixed/fixed end conditions will be 1 over 0.5 squared, which is 4 times the pinned-pinned test value. So, we see that the 36” buckling strength used to calculate the higher buckling strength of shorter braced intervals is somewhere between 2.0 and 4.0 times the buckling strength measured by pushing down on the end of a 36” stick. That’s a….pretty wide range. You can see why I said that using the 2.0 value is ‘conservative.’ Going to the next level of complexity gives us a way to narrow that range.
In the second link, we see the table for effective length factors for various end conditions has two columns, a “theoretical” value, and an “engineering effective length.” The engineering effective length recognizes that in real structures, a) end conditions aren’t perfect (exactly meeting all the assumptions that go into calculating them), and many other factors/complexities are at work in real structures. This link:
http://freeit.free.fr/Structure%20Engin ... ook/17.pdf
gives you, in mind-boggling depth, a sense of just how complicated these factors (and the associated math) really are when you dig into the science. See discussion in Sections 17.2 – 17.4 for effective length, and in Section 17.8 there is a discussion of bracing systems.. The key thing is Figure 17.2 on page 5. On page 5, this figure is explained as follows; “Figure 17.2 summarizes the theoretical K-factors (effective length) for columns with some idealized end conditions. The recommended K-factors are also shown in Figure 17.2 for practical design applications. Since actual column conditions seldom comply fully with idealized conditions used in buckling analysis, the recommended K-factors are always equal to or greater than their theoretical counterparts.”
These K-factors are the same shown in the second link. Since we’re dealing with real structures, it seems appropriate to use the “engineering”/”recommended” “K-“/”engineering effective length” factors.
Doing this, the ‘engineering’ K-factor for fixed-pinned end conditions is 0.8 (vs the 0.7071 theoretical factor we discussed and calculated from above). Doing the same calculation we did for 0.7071 ( which becomes 1 over 0.8 squared), we see that instead of multiplying the (pinned-pinned) push-down BS by 2.0, we would want to use a factor of 1.56. Looking at fixed-fixed end conditions, the ‘engineering’ K-factor is 0.65 (vs. the theoretical K-factor is 0.5. Doing the same calculation again (this time, 1 over 0.65 squared), we see that instead of multiplying the (pinned-pinned) push-down BS by 4.0, we want to use a factor of 2.37). So, instead of a range between 2.0 and 4.0 for the factor to adjust our 36” pushdown test data, we’re now at a range of 1.56 (if the end conditions of a braced leg segment are pinned-fixed) to 2.37 (if the end conditions of a braced leg segment are fixed-fixed).
So, the final question becomes, what are the end conditions of a braced section of leg in a tower? How does a tested 36” BS value (using single finger pushdown/pinned/pinned end conditions) correctly translate to a calculated BS of a leg section between two braced points? The answer is, I’m not sure, and the math to try to figure it is way, way over my head. I do know it is… effectively.. somewhere between.
When using the ‘ladders and Xs’ bracing approach I’ve detailed previously, it does seems like the braced leg segments have… something close to fixed end conditions at both ends (braced points), and it is pretty clear that neither end is under anything close to pinned end condition. And that’s why I’ve come to the conclusion that the correct approximation of the ‘real answer’ (what factor do you want to multiply 36” single finger pushdown measured buckling strength by to get to a buckling strength to use in calculating the buckling strength of braced leg segments in your tower) is somewhere between 2.0 and 2.3.
Only testing, in real towers, is going to give us insight into ‘the real answer.’ If the end conditions at braced points are really close to “fixed”, then the “best” tower weight estimates we’ve been tossing around out are a bit high; B-towers in the low to mid 6 gram, and C-towers at or slightly below 7.5 grams may be possible……
-
- Member
- Posts: 40
- Joined: Wed Feb 26, 2014 4:01 pm
- Division: C
- State: OH
- Has thanked: 0
- Been thanked: 0
Re: Measuring/using buckling strength-new info
Hi! First of all, thanks for going to such a length to address my situation! I was getting quite lost when I wasn't getting the same buckling strength values but this makes everything much clearer.
I'm still wrapping my head around the details, but your explanation for what caused the differences in our testing seems to make sense. I'll let you know if I have more questions. Thanks again!
I'm still wrapping my head around the details, but your explanation for what caused the differences in our testing seems to make sense. I'll let you know if I have more questions. Thanks again!
-
- Member
- Posts: 132
- Joined: Thu Oct 13, 2016 1:50 pm
- Division: C
- State: IL
- Has thanked: 0
- Been thanked: 0
Re: Measuring/using buckling strength-new info
Dang, this really changes the whole thing.. I can't even remember if I was using single finger pushdown to test the BS or not..
I might have to redo everything! :O
Just to make sure, would this mean I take the BS test normally with a single finger pushdown, and then multiply the number I get by the multiplier I calculate to get the final BS strength of something braced at a certain interval?
Like I would test with 1 finger (for example) to get say 40g BS, multiply by 2 so 80g, then braced at 5th interval so x80 ish to get it would be at 80x80 = 6400gBS? That's a huge difference!
I might have to redo everything! :O
Just to make sure, would this mean I take the BS test normally with a single finger pushdown, and then multiply the number I get by the multiplier I calculate to get the final BS strength of something braced at a certain interval?
Like I would test with 1 finger (for example) to get say 40g BS, multiply by 2 so 80g, then braced at 5th interval so x80 ish to get it would be at 80x80 = 6400gBS? That's a huge difference!
-
- Coach
- Posts: 1318
- Joined: Thu Nov 13, 2008 3:01 am
- Division: C
- State: CO
- Has thanked: 0
- Been thanked: 3 times
Re: Measuring/using buckling strength-new info
You're welcome; figured you and others might be in the same boat..... needed to be straightened out and clear.BananaPirate wrote:Hi! First of all, thanks for going to such a length to address my situation! I was getting quite lost when I wasn't getting the same buckling strength values but this makes everything much clearer.
I'm still wrapping my head around the details, but your explanation for what caused the differences in our testing seems to make sense. I'll let you know if I have more questions. Thanks again!
No, the one-finger pushdown value times 2 = the 36" BS you use to calculate shorter braced intervals. From our inverse square table, and using your 40/80 example, the multiplier for a 1/5 interval on a C-leg is 55.74.hearthstone224 wrote:Dang, this really changes the whole thing.. I can't even remember if I was using single finger pushdown to test the BS or not..
I might have to redo everything! :O
Just to make sure, would this mean I take the BS test normally with a single finger pushdown, and then multiply the number I get by the multiplier I calculate to get the final BS strength of something braced at a certain interval?
Like I would test with 1 finger (for example) to get say 40g BS, multiply by 2 so 80g, then braced at 5th interval so x80 ish to get it would be at 80x80 = 6400gBS? That's a huge difference!
We get this from length of 36" stick = 91.6cm. Length of leg = 61.34cm. 1/5 of leg length = 12.27cm. Proportion 1/5 of leg is of full 36" stick = 12.27/91.6, which = 0.134. 1 over 0.134 squared = 55.74.
So, if you get 40gr on a 1-finger test, first, multiply x 2 = 80gr (the BS at 36"). Braced at 1/5 interval (80gr x 55.74), the BS will 4460gr.
-
- Member
- Posts: 132
- Joined: Thu Oct 13, 2016 1:50 pm
- Division: C
- State: IL
- Has thanked: 0
- Been thanked: 0
Re: Measuring/using buckling strength-new info
Ah ok. That's kind of what I was trying to say, but thanks for confirming.
I think I'll have to redo everything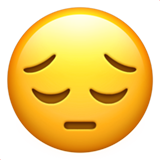
I think I'll have to redo everything
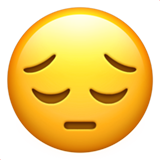
Re: Measuring/using buckling strength-new info
Can someone please explain this to me in a simpler matter? I'm having some trouble with the problem being addressed and I find this information highly valuable,thank you but I'm not sure I completely comprehend.
-
- Member
- Posts: 132
- Joined: Thu Oct 13, 2016 1:50 pm
- Division: C
- State: IL
- Has thanked: 0
- Been thanked: 0
Re: Measuring/using buckling strength-new info
Hey, first off welcome! I may not be the best at explaining this concept, but what we are currently doing is testing Bucking strength or as we like to call it, BS.
This is important to us because once we test BS, we can figure out which sticks we want to use in our final design.
Testing BS comes from taking a scale, taking a stick and pushing downwards (creating a sort of bow) and then trying to identify the number at which the scale sort of stays "stable" at. Balsa Man has made some changes to the process of getting the final calculation, but regardless of what the number is its a good idea to get a relative idea of which sticks are stronger than others.
Then, you can find the mass of each stick and you would try to identify the strong sticks that have a light weight on them. Those ones would be the sticks you would use.
Hope this helps!
This is important to us because once we test BS, we can figure out which sticks we want to use in our final design.
Testing BS comes from taking a scale, taking a stick and pushing downwards (creating a sort of bow) and then trying to identify the number at which the scale sort of stays "stable" at. Balsa Man has made some changes to the process of getting the final calculation, but regardless of what the number is its a good idea to get a relative idea of which sticks are stronger than others.
Then, you can find the mass of each stick and you would try to identify the strong sticks that have a light weight on them. Those ones would be the sticks you would use.
Hope this helps!
Re: Measuring/using buckling strength-new info
Thank you, also I was wondering what is the importance of braces? I know they are important although is it better to have more or less?
-
- Administrator
- Posts: 2416
- Joined: Sun Jan 05, 2014 3:12 pm
- Division: Grad
- State: WA
- Pronouns: He/Him/His
- Has thanked: 179 times
- Been thanked: 758 times
Re: Measuring/using buckling strength-new info
You want just the right amount. No braces mean major components are not fixed relative to one another and are more free to buckle or shift. Too many braces and you're making your tower heavier without significant additional structural improvement.Llamastwaimzjf wrote:Thank you, also I was wondering what is the importance of braces? I know they are important although is it better to have more or less?
How do you know if you have the right amount? Iteratively adjust your designs. If it keeps breaking somewhere, reinforce it there. If it never breaks somewhere, perhaps you don't need so many braces there.
"One of the ways that I believe people express their appreciation to the rest of humanity is to make something wonderful and put it out there." – Steve Jobs
-
- Coach
- Posts: 1318
- Joined: Thu Nov 13, 2008 3:01 am
- Division: C
- State: CO
- Has thanked: 0
- Been thanked: 3 times
Re: Measuring/using buckling strength-new info
Back on page 2 of the Towers B/C thread, in September, I provided a discussion about this. Worth bring into this thread for....convenience. Here's that post, with a few additional things added, in italics, and underlining for emphasis of important points, for completeness and clarity:Llamastwaimzjf wrote:Thank you, also I was wondering what is the importance of braces? I know they are important although is it better to have more or less?
Quick review of three basic mathematical relationships that might help everyone, re discussion on leg angles, and the effects of those angles, and what the bracing of legs is all about. These apply to both tower legs, and the outer/end legs of bridges, btw… If you dig back through the archives, you’ll find plenty of detailed discussion (re: towers, bridges, and booms).
First, forces on a leg. For discussion, lets assume a 4-leg tower. Having not gotten this year’s rules yet, don’t know what the size of the hole in the test base the legs need to clear/be outside of.
So, let’s start with a simple case- a … hypothetical straight tower; legs vertical, on the corner of a 5cm square (so the 5cm square load block just sits/fits on top). With a 15kg load, each leg will carry 1/4th of that load- a 3.75 kg “axial compressive” force (i.e., the load puts a compressive force along the long axis of each leg). If the force is strong enough, or the leg weak enough, it will fail by “buckling”- the middle will bow outward due to the force, and the leg will break.. Having one leg buckle is the most common way towers will fail under load. If there's much load on (sand in the bucket), it will happen VERY quickly- bang, one leg will snap, the portion of the tower above that break point will lean toward the broken leg, the load block will pull straight down through ....the wreckage, breaking other pieces
So what happens/what’s the math, if the legs are angled (wider at the base/bottom- to clear the defined base opening)? As discussed above, the “more angled” the legs are, the greater the force they have to carry (at a given load). If you do a vector analysis, you’ll find that force has an “inverse cosine “ relationship to the angle from vertical- the force is 1 over the cosine (1/cos) of the angle from vertical, times the load. If you drop an imaginary vertical line from the top of one leg down to the test base, you form a right triangle. The hypotenuse of that triangle is the leg. The imaginary vertical line is the other (adjacent) side of the angle from vertical. The cosine of the angle between the hypotenuse and the adjacent side is the length of the adjacent side divided by the length of the hypotenuse.
Looking at a few cosine values, 1/cos, and axial compressive force on one leg of a four leg tower with a 15 kg load
0 degrees; cosine = 1.0000; 1/cos = 1.000; axial compressive force = 3.75 kg
5 degrees; cosine = 0.9962; 1/cos = 1.0038; axial compressive force = 3.78 kg
10 degrees; cosine = 0.9847; 1/cos = 1.0155; axial compressive force = 3.81 kg
15 degrees; cosine = 0.9661; 1/cos = 1.0351; axial compressive force = 3.88 kg
20 degrees; cosine = 0.9397; 1/cos = 1.0642; axial compressive force = 3.99 kg
30 degrees; cosine = 0.8658; 1/cos = 1.1550; axial compressive force = 4.33 kg
The bottom line, until that angle gets pretty big, the effect of the angle on the force on the leg is pretty small. Even at 30 degrees from vertical, the increase in force (from that on a vertical leg) is about 15%
In a B-div tower, the leg angles for a tower qualifying for the 29cm circle bonus are abour 12.5 degrees, for a C tower, about 10.5 degrees.
And here's the discussion that relates to your question:
The second important relationship to understand is how the strength of a leg (resisting buckling) relates to its length. This is an “inverse square” relationship. Google up Euler’s Buckling Theorem to see the formula. What its saying is that if you have a column- a leg- a piece of wood say 60cm long, and it has a buckling strength of 0.5 kg, if you cut its length to 1/2, to 30 cm, its buckling strength goes up by a factor of 4 (to 2.0 kg); if you cut its length to 1/3, to 20 cm, its buckling strength goes up by a factor of 9 (to 4.5 kg). (this is what the bracing does- by bracing, you increase the leg strength)
You can see/get a feel for this important relationship by taking a (nice straight) balsa stick, place it on a scale, vertically, and push straight down. At some force/load, the middle will start to bow out (buckle)- that’s its buckling strength at that length. Be careful not to break it; just note/see the force/weight measured by the scale when it starts to buckle. Now, cut the stick in half, and do the same “axial loading” to the point buckling starts, and you’ll see the force on the scale is about 4 times what it was at full length. The numbers you get won’t be perfect; there will be some variation in the stiffness along/within the stick (that’s just the nature of wood- its not perfect/homogeneous), and its likely not perfectly straight, and without a pretty precise testing setup, the force you put on the top won’t be perfectly vertical, but you will see pretty close to 4 times the buckling strength.
What the bracing between the legs is all about is turning the long leg/column (with a low buckling strength) into a set of shorter, equal length, “stacked columns” (with much higher buckling strength). You can get a feel for this by repeating the ‘push down on a long stick on the scale” drill. Mark the midpoint on the stick- push down at full length, note the weight/load at which buckling starts. Now, push it to the start of buckling again, but with your other hand, hold the midpoint in place, so it doesn’t move in space, and what you’ll see is that at about 4 times the long length buckling load, one of the sections (above or below your fingers holding/bracing the midpoint) will start to buckle. There is good, detailed discussion in the forum archives on approaches to doing the bracing. Key is keeping the “braced interval” equal- if the exposed section of the leg between braced points is unequal, the longer exposed leg segment will break first. In other words, you do bracing at 1/2, 1/3, 1/4, 1/5 intervals- 1 bracing set at midpoint of legs, 2 bracing sets at 1/3 points of legs, 3 bracing sets at 1/4 point, etc. That way, there's no "weak link" (a longer exposed segment, that will break prematurely).
On page 10 of the Towers B/C thread, I provided a post, with an attachment explaining how bracing works and providing drawings, and it explains in detail how to do one type/system of bracing, called 'Xs and ladders."
The third/last important relationship to understand is the effect of density on the stiffness of a leg. This is pretty close to a linear relationship; if you have two sticks w/ the same size/cross section (e.g. 1/8” x 1/8”), and one weighs twice what the other weighs, the heavier one will have about twice the buckling strength at a given length. ( http://ir.library.oregonstate.edu/xmlui ... /1957/1286 ). Heavier sticks are stiffer/stronger. The basic design problem is figuring out what gets you to the lightest tower weight that will hold close to the 15gk max load; heavier, stiffer legs, with few/fewer bracing intervals/sets, or lighter, floppier/weaker legs, with more bracing intervals/sets to brace them enough for them to carry max load. There is very detailed discussion in the Towers B/C thread about how to analyze this fundamental design trade-off.
Understanding these basic relationships gives you the basis for designing an efficient tower.