
And, as to whether to use a tower or not more than once... I think it really depends on the design.
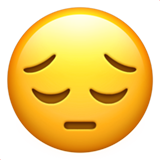
We usually compete at tournaments using pre-tested structures. A few years ago, for Elevated Bridge, we pre-tested our competition bridge many times (around 100 times). The pre-tested bridge earned us 1st place at the state tournament and fifth place at the nationals that year. The repeated testing was easy for a short structure (the bridge was only 30 cm in height) using a commercial testing apparatus that uses a force gauge. The apparatus allowed us to load an unload the structure in a matter of seconds; we did the 100 loading cycles in less than one hour.mrsteven wrote:Here's a question I just thought of...
When you build bridges and test them, if it holds all the weight and your totally happy about its weight, do you use it again? Or because you put force onto it, its weaker than before?
I agree, I can understand 1 or 2 times but any more than that seem redundantjma wrote:Hi SLM,
What is the purpose of pre-test the same structure several times?
Good question.jma wrote:Hi SLM,
What is the purpose of pre-test the same structure several times?
Yeah, testing is the only way to know for sure.jma wrote:Thanks for your response.
For new builders like us, if we don't know how to calculate the capacity of our tower,the only way to know is to test until our tower breaks or is there a better way?
Calculating the load carrying capacity of a tower is a challenging task, even for experienced builders. Using physics/engineering, you can estimate the strength of your tower design with 80% to 85% accuracy. Beyond that, you need to resort to testing to more accurately determine how much load the tower can hold.jma wrote:Thanks for your response.
For new builders like us, if we don't know how to calculate the capacity of our tower,the only way to know is to test until our tower breaks or is there a better way?
Using a testing platform that limits the amount of failure to one member at a time is a good idea for sizing structural members. As Balsa Man suggested, you can load the tower until a member fails, strengthen the member by increasing its size, then test the tower again. This technique is particularly effective as long as the re-built member is not significantly larger in size (stronger) than the original member. Why do I say that? Because by increasing the size of the member you are increasing its stiffness. Generally (although there are some exceptions) stiffer members in a structure are forced to carry more of the load. So by changing the size of the failed member, you are in effect changing the load distribution pattern in the structure. That is, most member forces in the revised structure are not the same as the member forces in the original structure. Therefore, the technique could lead to an over-designed tower.Balsa Man wrote:As I noted in my earlier post today, a safety tower gets you around the problem of destroying a tower in testing. That's why I referred to it as a "development tool." ...