Oh shoot yeah my bad. I wonder if the carbon was actually 6.3mm squares because I applied this "+0.25mm" rule to alot of my 3D prints and it has held true for almost all. Of course this will vary depending on extruder temperature, heated/unheated build plate, material, etcPM2017 wrote:Isn't that 0.35 mm?windu34 wrote:I would recommend at least 4-5cm for the depth of the hole (I think mine were actually more like 7-8cm). And yes it requires some trial and error. The advertised CF I used was 6.2mm square and my 3D printed squares were 6.55mm for a perfect press-fit. I found that adding 0.25mm when printing with PLA was pretty optimal
Battery Buggy B
-
- Staff Emeritus
- Posts: 1382
- Joined: Sun Apr 19, 2015 6:37 pm
- Division: Grad
- State: FL
- Has thanked: 2 times
- Been thanked: 37 times
Re: Battery Buggy B
Boca Raton Community High School Alumni
University of Florida Science Olympiad Co-Founder
Florida Science Olympiad Board of Directors
kevin@floridascienceolympiad.org || windu34's Userpage
University of Florida Science Olympiad Co-Founder
Florida Science Olympiad Board of Directors
kevin@floridascienceolympiad.org || windu34's Userpage
-
- Member
- Posts: 524
- Joined: Fri Jan 20, 2017 5:02 pm
- Division: Grad
- State: CA
- Has thanked: 23 times
- Been thanked: 13 times
Re: Battery Buggy B
It might have been 6.35mm since that is a quarter inch.windu34 wrote:Oh shoot yeah my bad. I wonder if the carbon was actually 6.3mm squares because I applied this "+0.25mm" rule to alot of my 3D prints and it has held true for almost all. Of course this will vary depending on extruder temperature, heated/unheated build plate, material, etcPM2017 wrote:Isn't that 0.35 mm?windu34 wrote:I would recommend at least 4-5cm for the depth of the hole (I think mine were actually more like 7-8cm). And yes it requires some trial and error. The advertised CF I used was 6.2mm square and my 3D printed squares were 6.55mm for a perfect press-fit. I found that adding 0.25mm when printing with PLA was pretty optimal
Do you recall which print settings and filament company you used?
West High '19
UC Berkeley '23
Go Bears!
UC Berkeley '23
Go Bears!
-
- Exalted Member
- Posts: 774
- Joined: Sun Nov 19, 2017 9:09 am
- Division: C
- State: RI
- Has thanked: 211 times
- Been thanked: 56 times
Re: Battery Buggy B
Ok, I have embarked on my quest for the perfect F1 Battery Buggy
! I 3d printed this file I designed in Tinkercad:
https://www.tinkercad.com/things/gvUEjg ... WOcrcBWqc=
My 8 mm square CF rod fits almost perfectly in the top square hole of the test print, but it is able to wiggle a little bit in the two bottom square holes. Is this normal?
The dimensions of each square hole are all the same: 8 mm side by 8 mm side by 1 cm depth. The hole in the middle is for the ball bearings.
Also, my test print came out a little bit warped. Not sure if that may be a problem.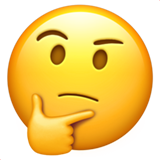
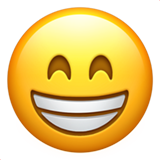
https://www.tinkercad.com/things/gvUEjg ... WOcrcBWqc=
My 8 mm square CF rod fits almost perfectly in the top square hole of the test print, but it is able to wiggle a little bit in the two bottom square holes. Is this normal?
The dimensions of each square hole are all the same: 8 mm side by 8 mm side by 1 cm depth. The hole in the middle is for the ball bearings.
Also, my test print came out a little bit warped. Not sure if that may be a problem.
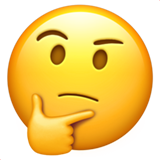
-
- Exalted Member
- Posts: 774
- Joined: Sun Nov 19, 2017 9:09 am
- Division: C
- State: RI
- Has thanked: 211 times
- Been thanked: 56 times
Re: Battery Buggy B
Something is starting to bother me as well. Let me explain why. In the last post I mentioned that the rods could wiggle a little bit. windu used 3 CF rods on the bottom of his 2016 EV. And in a previous post windu described some sort of chassis torsion.
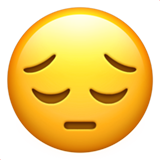
Is 2 mm of ABS enough to keep the CF from breaking free of the 3D printed connector (see Tinkercad file)? And do the 2 rods on the bottom provide sufficient strength to hold my Battery Buggy together? Maybe I should put 3 on the bottom like windu did. The torsion thing is making me very nervous...windu34 wrote: This is NOT a good reason to go with this design lol
The correct reasons are as follows:
Benefits: Elimination of chassis torsion and it allows for implementation of passive adjustable steering (as seen on EV 2016)
Cons: Difficult to implement correctly - fit between CF and 3D printed parts MUST be an interference fit or you WILL run into problems (you cant just glue/epoxy the rods in - the fit needs to be so tight that you have to lube the rods and hammer them in.
These pros/cons are not self-evident and i didnt realize them until I struggled with chassis torsion on my 2017 EV which required a complicated solution to solve.
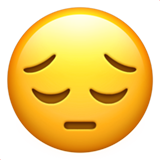
-
- Exalted Member
- Posts: 774
- Joined: Sun Nov 19, 2017 9:09 am
- Division: C
- State: RI
- Has thanked: 211 times
- Been thanked: 56 times
Re: Battery Buggy B
First, an apology for asking so many questions (planning phase). Next, I would like to run this idea through you guys. Say I 3D print an attachment for my motor, and I either drill holes or have the holes "pre-made". Can I fill the holes in with hot glue, and then use a couple of wood screws to secure my Pololu 25D mounting bracket to the 3d printed part?
-
- Member
- Posts: 438
- Joined: Mon Oct 09, 2017 6:25 pm
- Division: C
- State: NJ
- Has thanked: 1 time
- Been thanked: 0
Re: Battery Buggy B
You can't screw directly into the abs, it will warp and everything will go wrong. if its pla, it will just shatter. U need to have threaded holes in your design.
-
- Exalted Member
- Posts: 774
- Joined: Sun Nov 19, 2017 9:09 am
- Division: C
- State: RI
- Has thanked: 211 times
- Been thanked: 56 times
-
- Member
- Posts: 271
- Joined: Mon Mar 12, 2018 9:35 am
- Division: C
- State: IN
- Has thanked: 1 time
- Been thanked: 6 times
Re: Battery Buggy B
Screwing into hot glue is definitely not advised. Not only would everything melt, but anything placed into that hole would have very little support.MadCow2357 wrote:I wouldn't be screwing into ABS. I would be screwing into cooled hot glue.
2018: Battery Buggy, Road Scholar, Roller Coaster
2019: Chem Lab, Code, Disease, Fossils, Geo Maps, Sounds
2020 and 2021: Astro, Chem Lab, Code, Fossils, Geo Maps, Sounds
When you miss nats twice by a combined two points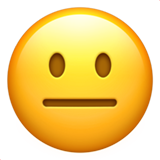
2019: Chem Lab, Code, Disease, Fossils, Geo Maps, Sounds
2020 and 2021: Astro, Chem Lab, Code, Fossils, Geo Maps, Sounds
When you miss nats twice by a combined two points
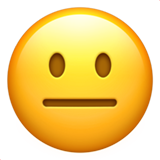
-
- Exalted Member
- Posts: 774
- Joined: Sun Nov 19, 2017 9:09 am
- Division: C
- State: RI
- Has thanked: 211 times
- Been thanked: 56 times
Re: Battery Buggy B
So I can't mount my micro switch like that?hippo9 wrote:Screwing into hot glue is definitely not advised. Not only would everything melt, but anything placed into that hole would have very little support.MadCow2357 wrote:I wouldn't be screwing into ABS. I would be screwing into cooled hot glue.
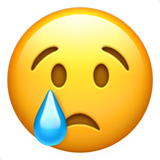
-
- Exalted Member
- Posts: 774
- Joined: Sun Nov 19, 2017 9:09 am
- Division: C
- State: RI
- Has thanked: 211 times
- Been thanked: 56 times
Re: Battery Buggy B
MadCow2357 wrote:Ok, I have embarked on my quest for the perfect F1 Battery Buggy! I 3d printed this file I designed in Tinkercad:
https://www.tinkercad.com/things/gvUEjg ... WOcrcBWqc=
My 8 mm square CF rod fits almost perfectly in the top square hole of the test print, but it is able to wiggle a little bit in the two bottom square holes. Is this normal?
The dimensions of each square hole are all the same: 8 mm side by 8 mm side by 1 cm depth. The hole in the middle is for the ball bearings.
Also, my test print came out a little bit warped. Not sure if that may be a problem.